Quick and Reliable Product Packaging Equipment Repair Service Services to Minimize Downtime
In the competitive landscape of production, the performance of packaging operations pivots on the integrity of machinery. Quick and trustworthy repair services are crucial in reducing downtime, which can lead to significant operational obstacles and economic losses.
Relevance of Timely Repairs
Timely repairs of product packaging makers are critical for keeping functional performance and decreasing downtime. In the hectic environment of manufacturing and product packaging, also small malfunctions can result in considerable delays and efficiency losses. Dealing with issues quickly guarantees that equipments run at their optimum capability, consequently securing the flow of operations.
Additionally, timely and regular upkeep can stop the acceleration of small troubles right into major breakdowns, which usually sustain higher repair prices and longer downtimes. A positive method to machine fixing not only maintains the honesty of the devices but additionally improves the overall integrity of the manufacturing line.
Furthermore, timely fixings add to the longevity of product packaging machinery. Machines that are serviced immediately are less most likely to struggle with too much deterioration, permitting organizations to maximize their financial investments. This is particularly important in markets where high-speed packaging is vital, as the requirement for regular performance is extremely important.
Benefits of Reliable Company
Trustworthy company play a critical duty in guaranteeing the smooth procedure of packaging machines. Their expertise not only boosts the efficiency of repair services but additionally contributes substantially to the longevity of equipment. Trusted provider are furnished with the technical understanding and experience essential to diagnose issues precisely and apply efficient solutions rapidly. This minimizes the threat of recurring problems and guarantees that machines operate at ideal efficiency degrees.
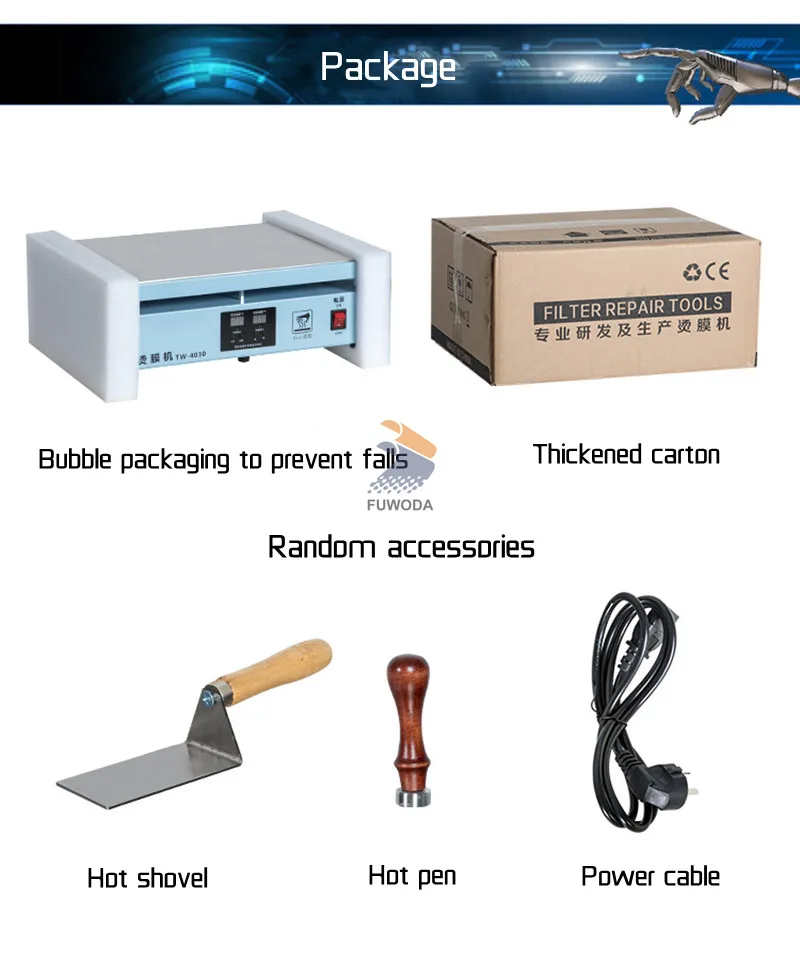
In addition, a trusted service supplier uses thorough support, including training and guidance for staff on machine procedure and upkeep ideal techniques. This not just encourages staff members however also grows a society of security and effectiveness within the company. In general, the benefits of engaging dependable provider extend past instant repairs, favorably influencing the whole operational process of packaging processes.
Usual Product Packaging Device Issues
In the world of packaging procedures, various problems can compromise the effectiveness and functionality of equipments (packaging machine repair). Another usual issue is misalignment, which can create jams and uneven product packaging, influencing product top quality and throughput.
Electrical issues can additionally interrupt product packaging procedures. Faulty electrical wiring or malfunctioning sensing units may lead to irregular device habits, triggering hold-ups and enhanced functional prices. Additionally, software application problems can hinder the equipment's programs, causing functional inefficiencies.
Inconsistent product circulation is an additional essential problem. This can develop from variants in item shape, size, or weight, which might affect the machine's capability to manage products properly. Ultimately, insufficient training of operators can exacerbate these issues, as inexperienced employees might not recognize early indications of malfunction or may misuse the devices.
Attending to these typical product packaging maker problems immediately is important to maintaining productivity and ensuring a smooth procedure. Normal assessments and positive maintenance can significantly mitigate these concerns, cultivating a reliable product packaging atmosphere.
Tips for Lessening Downtime
To reduce downtime in product packaging procedures, carrying out a positive maintenance approach is vital. On a regular basis arranged upkeep checks can recognize prospective issues prior to they intensify, ensuring equipments run efficiently. Developing a routine that consists of lubrication, calibration, Click This Link and assessment of crucial components can substantially lower the regularity of unexpected failures.
Training team to run equipment properly and identify early indication of malfunction can likewise play a vital function. Empowering operators with the understanding to perform standard troubleshooting can avoid small issues from triggering significant hold-ups. In addition, maintaining an efficient supply of vital extra parts can accelerate repair services, as waiting for components can lead to prolonged downtime.
Additionally, documenting maker efficiency and upkeep activities can aid identify patterns and frequent troubles, allowing for targeted treatments. Incorporating advanced tracking modern technologies can provide real-time data, allowing anticipating maintenance and reducing the danger of unexpected failings.
Last but not least, cultivating open interaction in between drivers and upkeep groups ensures that any irregularities are quickly reported and attended to. By taking these positive procedures, organizations can boost functional performance and dramatically reduce downtime in product packaging procedures.
Selecting the Right Fixing Solution
Selecting the ideal repair work service for product packaging equipments is an important decision that can significantly impact functional performance. Begin by examining the company's experience with your particular kind of packaging equipment.
Following, consider the solution company's reputation. Seeking feedback from various other organizations within your sector can provide insights right into dependability and top quality. Accreditations and partnerships with identified equipment suppliers can also suggest a dedication to excellence.
In addition, analyze their action time and availability. A company who can use prompt support reduces downtime and maintains production flow consistent. It's additionally important to ask about warranty and service warranties, which can mirror the confidence the supplier has in their job.
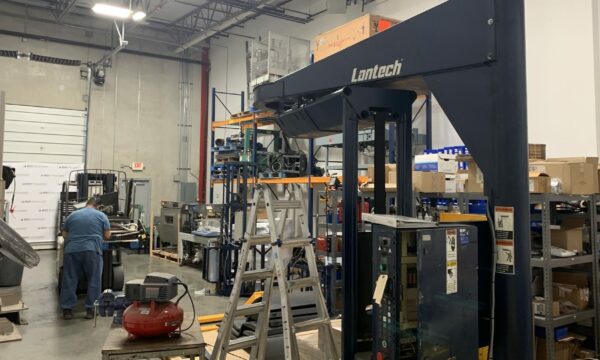
Verdict
To conclude, the value of quick and dependable packaging machine fixing services can not be overemphasized, as they play an important role in decreasing downtime and making sure operational performance. By prioritizing prompt repairs and picking reliable solution suppliers, businesses can successfully maintain and attend to common problems productivity. Carrying out proactive maintenance techniques and buying team training additional boosts the longevity of product packaging equipment. Eventually, a critical my site method to repair solutions fosters a much more resistant production atmosphere.
Timely repair work of product packaging makers are critical for maintaining functional performance and minimizing downtime.Additionally, timely repair work contribute to the durability of packaging machinery. On the whole, the benefits of involving reliable service carriers expand past prompt fixings, favorably impacting the entire operational workflow of product packaging procedures.
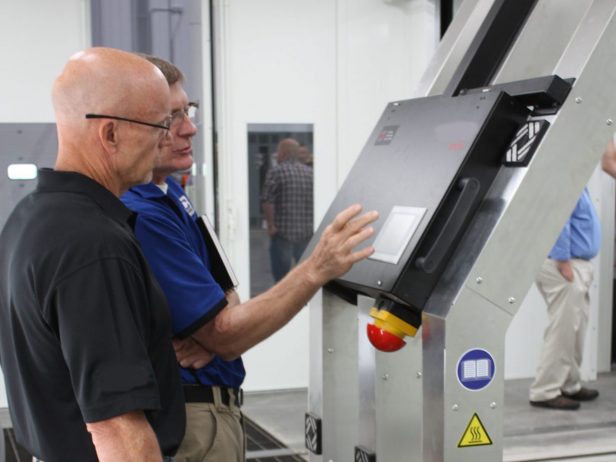
Comments on “Maximizing Equipment Efficiency Through Packaging Machine Repair”